As a logistics company, you understand the importance of delivering the right products to the right place at the right time. The success of your logistics business depends on optimizing your processes to ensure efficiency, productivity, and profitability. However, achieving these goals can be challenging in a competitive and dynamic market. This blog will provide you with essential tips for optimizing processes in your logistics business to stay ahead of the competition.
Use Technology to Streamline Operations
One of the most effective ways to optimize processes in your logistics business is by using technology. There are many software solutions available that can help streamline your operations and boost productivity. Here are four of the best ones you should consider investing in:
Transportation Management Systems (TMS)
A TMS is a software solution that helps you manage all aspects of the transportation process, from planning and executing shipments to tracking and reporting. With a TMS, you can easily assign carriers, monitor freight costs, and track inventory levels in real time. This not only increases efficiency but also reduces human error.
Warehouse Management Systems (WMS)
A WMS is a software solution that helps you manage all activities within your warehouse, from receiving to picking and shipping. With a WMS, you can automate processes such as inventory management, order fulfillment, and labor tracking, making your operations more efficient and accurate.
Route Planning Software
Route planning software is an essential tool for logistics companies that need to optimize their delivery routes. This software uses advanced algorithms to calculate the most efficient and cost-effective routes for your drivers, taking into account factors such as traffic patterns, delivery windows, and vehicle capacities. By optimizing your routes, you can reduce transportation costs and improve on-time deliveries.
Electronic Data Interchange (EDI)
EDI is a technology that allows businesses to exchange documents electronically in a standardized format. By implementing EDI, you can automate data entry and communication with your partners, suppliers, and customers. This not only improves accuracy but also reduces the time it takes to process orders and invoices, making your operations more efficient.
Using technology can also help you track shipments, monitor performance, and analyze data for better decision-making.
Choose the Right Vehicles
Another way to optimize processes in your logistics business is by choosing the right vehicles for your fleet. Factors such as fuel efficiency, cargo capacity, and maintenance costs should be considered when selecting vehicles for your operations. Investing in modern and efficient vehicles can improve delivery times, reduce transportation costs, and increase customer satisfaction.
A modern wing van truck, for example, is designed for efficient loading and unloading, reducing the time it takes to complete deliveries. It also has a larger cargo capacity, allowing you to transport more goods in one trip. Investing in the right vehicles not only streamlines your operations but also helps you stay competitive in the market.
Focus on Customer Service
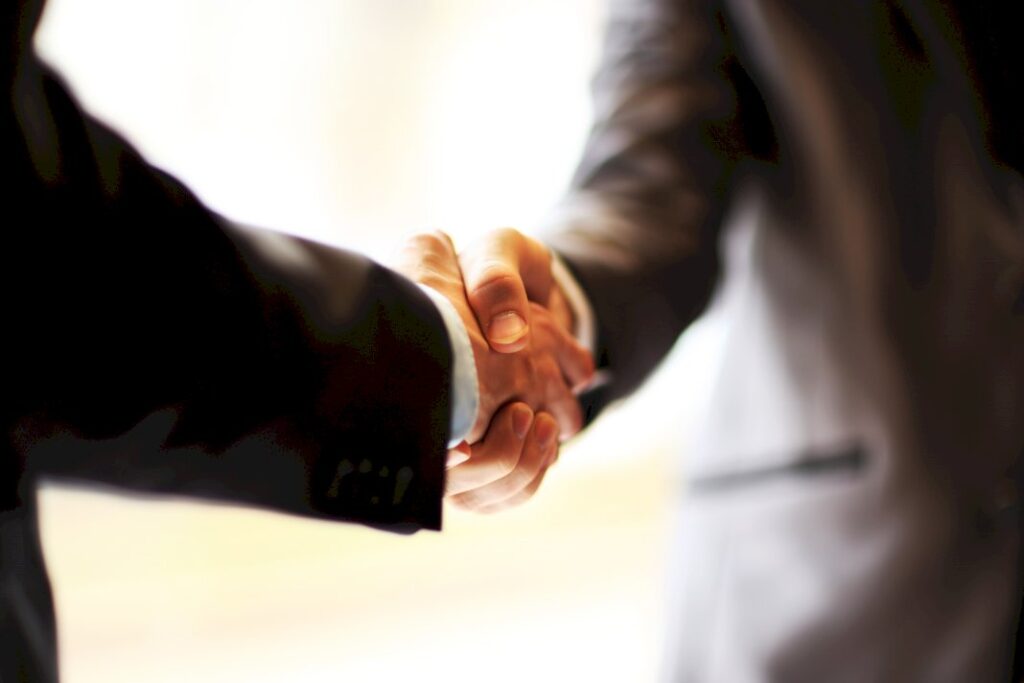
Your logistics business cannot succeed without satisfied customers. Therefore, optimizing your processes should also involve focusing on customer service. This means ensuring timely and accurate deliveries, providing personalized support, and responding promptly to inquiries and complaints. With good customer service, you can enhance your reputation and retain loyal clients who will recommend your services to others.
Implement Lean Principles
Lean management is a philosophy that emphasizes maximizing value while minimizing waste. Applying lean principles to your logistics business can help you eliminate inefficiencies, reduce costs, and improve quality.
For example, you can use the 5S methodology to organize your workspace and reduce clutter or implement just-in-time (JIT) inventory management to reduce excess inventory and improve cash flow. Lean principles can also enhance collaboration, innovation, and employee engagement.
Measure and Analyze Performance
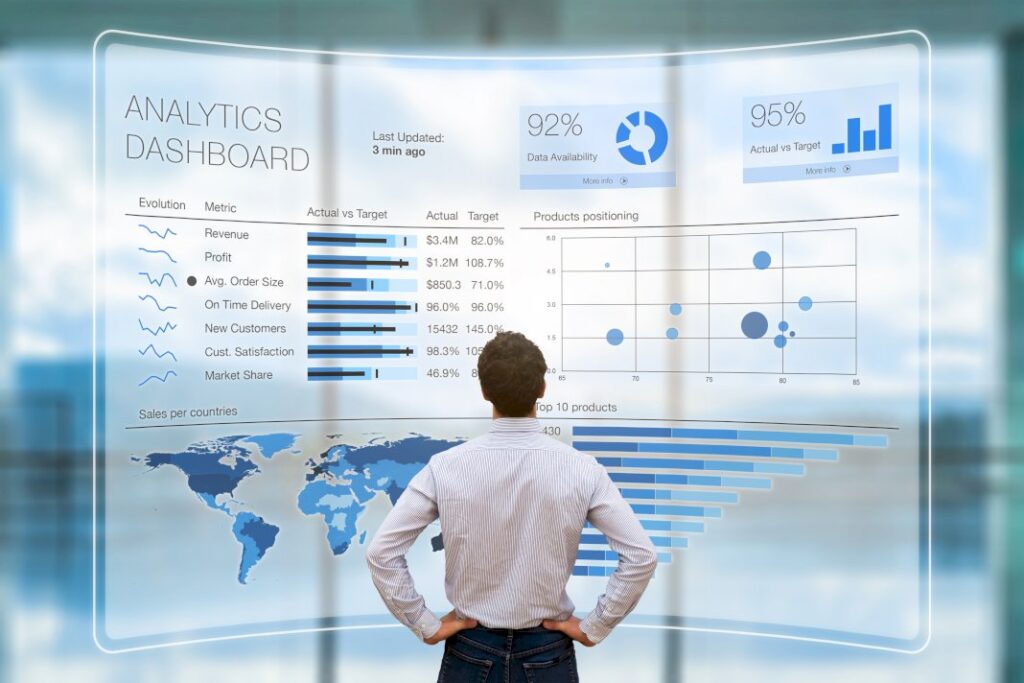
To optimize your processes, you must measure and analyze performance. This means setting clear objectives, defining key performance indicators (KPIs), and monitoring progress regularly. KPIs may include delivery time, order accuracy, inventory turnover, or customer satisfaction.
Analyzing data and performance can help you identify areas for improvement, implement corrective actions, and measure the impact of your changes. Performance measurement can also foster a culture of accountability, collaboration, and continuous improvement.
Optimizing processes in your logistics business involves a multi-faceted approach that combines the use of technology, selection of efficient vehicles, focus on customer service, implementation of lean principles, and regular performance measurement and analysis. By embracing these strategies, you can drive efficiency, improve productivity, and enhance profitability.
Remember, the key to staying ahead in the competitive logistics industry is constant improvement and adaptation. Remain alert to new trends and advancements, and be prepared to embrace transformative changes to continue growing. With these tips in your arsenal, you’re well-equipped to navigate the challenges and opportunities that lie ahead in the logistics landscape.
For more valuable information visit our website.